In unserer Rubrik „Aus dem Südwesten“ stellen wir Produkte vor, die viele kennen, von denen aber wenige wissen, dass sie in der Region hergestellt werden.
Diesmal: Heizungen für Wasserbetten, hergestellt von der Carbon Heater GmbH aus Bad Dürrheim.
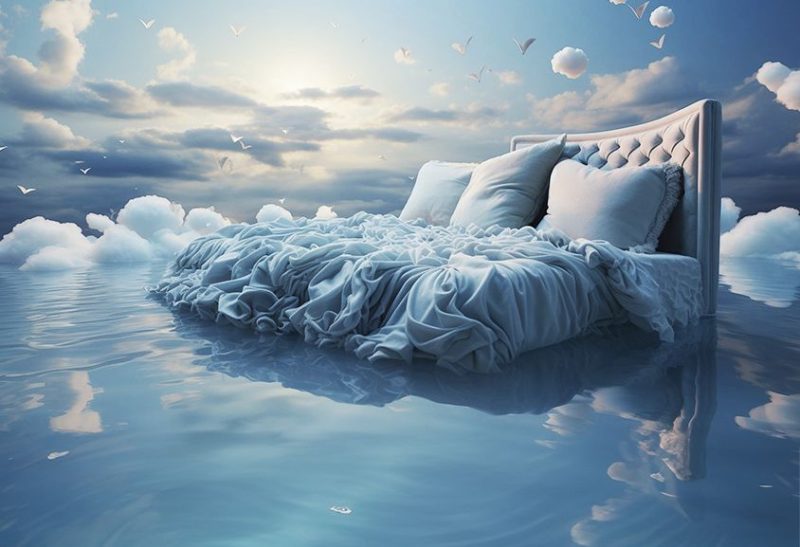
Konkurrenz für die Platzhirsche
Angeblich sorgt es für hohen Liegekomfort und erholsamen Schlaf, ist besonders weich, allergikerfreundlich und kuschelig warm. Das Wasserbett. Andrejel Zajac, Geschäftsführer der Carbon Heater GmbH in Bad Dürrheim, und sein Bruder und Mitgeschäftsführer Miko Zajac haben das Potenzial dieser Branche erkannt: „2003 fragte uns ein Wasserbettenhändler: ‚Wäre es möglich, für mich eine Wasserbettenheizung zu entwickeln und zu produzieren?‘“ Beim Brainstorming und nach einer Marktrecherche stellten die Brüder fest, dass es in diesem Bereich nur wenig Wettbewerber gab. „Eigentlich nur zwei Platzhirsche und das, obwohl es ein relativ großer Markt ist“, resümiert Andrejel Zajac, der damals noch bei einem großen Bankhaus tätig war. „Und so haben wir den Startknopf gedrückt und Carbon Heater gegründet.“
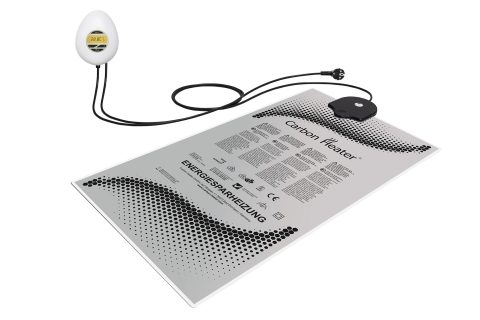
Weltweit vertreten
Miko Zajac war von Anfang an für die Entwicklung zuständig, Andrejel Zajac für die Vermarktung. Die Fertigung der Produkte war in den ersten Jahren komplett outgesourct. „Das war eine logistische Herausforderung, funktionierte jedoch bis Ende 2009 sehr gut“, erinnert sich Andrejel Zajac. „An unserem Hauptsitz in Villingen-Schwenningen kümmerten wir uns um Technik, Materialbeschaffung und Vermarktung.“ Doch der Absatz stieg enorm und so entstand 2010 die erste eigene Produktionsstätte in VS-Schwenningen. Als nach weiteren zehn Jahren der Platz zu knapp wurde, zog Carbon Heater an seinen heutigen Standort in Bad Dürrheim. Inzwischen beliefert das Unternehmen hauptsächlich Wasserbettenhersteller der gehobenen Mitte- und Premiumklasse mit seinen Heizsystemen. Pro Woche werden bis zu 1.000 Stück produziert, Bestseller ist die analog geregelte „Classic“-Heizung, die rund 70 Prozent der Produktionsmenge in diesem Bereich ausmacht. Kunden sind weltweit zu finden. Carbon Heater exportiert nach Firmenangaben mit einem Marktanteil von circa 65 Prozent in insgesamt 32 Länder, primär nach Europa, Australien, Neuseeland und China. Neben den Wasserbettheizungen entwickelt und produziert das Unternehmen weitere Heizapplikationen für Umwelt- und Simulationsanlagen, Maschinenbau, Foodtechnik (Speisenregenerierung) sowie Tischklimageräte für Arbeitsplätze.
Wie die Schweizer Alpen
Das Heizelement von Carbon Heater besteht aus unterschiedlichen Polyesterfolienlagen. „Die Trägerfolie, auf welche der Heizwiderstand – also das Carbon (Kohlenstoff) und die Silberelektrode beschichtet werden – ist plasmabehandelt“, erklärt Miko Zajac. Durch diese Behandlung wird die Oberfläche der Folie vergrößert. „Unter einem Mikroskop sieht das dann ein bisschen aus wie die Schweizer Alpen“, beschreibt er bildhaft. Nach der Beschichtung kommt die Folie für 24 Stunden in einen Temperofen, wodurch sich Heizwiderstand, Elektrode und Folien dauerhaft verbinden und eine Einheit bilden. Es folgen weitere Folienschichten: Schutzisolation, Aluminiumabschirmung, wasserfeste Ummantelung und schließlich die Beschriftung.
Nieten statt löten
Um das Heizelement auch nutzbar zu machen, muss es noch mit Temperaturfühler, Schutzbegrenzer und Steuerleitung verbunden werden. „Üblicherweise erfolgt die Kontaktierung durch Löten. Wir haben uns jedoch dafür entschieden, maschinell zu nieten, um so eine hohe Prozesssicherheit zu gewähren, da wir bei Lötstellen nicht immer eine gleichbleibend hohe Qualität garantieren können“, erläutert Miko Zajac. Zur Bedienung des fertigen Heizelements benötigt es nun noch eine elektronische Regelung. Neben der analogen Regelung bietet Carbon Heater auch eine digitale Version an, mit Netzfreischaltungstauglichkeit und integrierter zweipoliger Zeitschaltuhr, die auch wecken kann oder meldet, wenn das Pflegemittel nachgefüllt werden soll. „Wie alle unsere Steuerungen sind auch diese von uns entwickelt und dimensioniert“, so der Geschäftsführer. Bestückt wird die Platine von externen Partnern in Deutschland. Sind alle Baugruppen vor Ort, werden sie geprüft und in die entsprechenden Gehäuseteile montiert. „Zuletzt erfolgt eine vollumfängliche Prüfung von Heizelement und Regelung, ehe das Ganze an den Distributor geliefert wird, der wiederum seine Händler und Endkunden versorgt.“
Text: Andrea Keller
Bild: (oben) Adobe Stock/Adam