„Gutex ist der Mercedes unter den Holzfaserdämmstoffherstellern – wir sind Qualitäts- und Innovationsführer“, sagt Geschäftsführer Claudio Thoma. Die Produkte des Familienunternehmens aus Waldshut-Tiengen kommen im Neubau sowie bei der Sanierung von Gebäuden zum Einsatz, vor allem im Dach, aber auch in der Fassade und im Boden. Rund 60 Millionen Euro hat Gutex 2017 umgesetzt, das ist ein Plus von zwölf Prozent im Vergleich zu 2016 und dreimal so viel wie 2005.
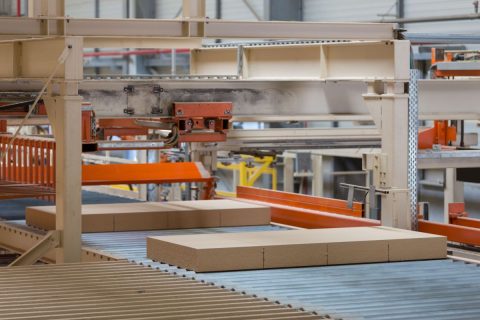
Gutenburg. Hackschnitzel türmen sich zu Hügeln auf dem Betriebsgelände der Gutex Holzfaserplattenwerk H. Henselmann GmbH & Co. KG in Gutenburg, einem kleinen Ortsteil von Waldshut-Tiengen. Wasserdampf steigt in weißen Säulen aus den Produktionsgebäuden in das enge Schlüchttal auf, durch das sich der gleichnamige Fluss seinen Weg gebahnt hat. Über die Schlücht werden die Hackschnitzel auf Förderbändern in die verschiedenen Produktionshallen transportiert. Dort liegt Holzgeruch in der Luft. In einer Halle werden aus Hackschnitzeln im sogenannten Nassverfahren etwa 2,5 Zentimeter dicke Platten hergestellt, die später als Trittschall unter Laminat oder Parkett verlegt werden. In einer anderen Halle entstehen an diesem Wintertag im sogenannten Trockenverfahren etwa zehn Zentimeter dicke Ultrathermplatten für die Dachsanierung. Rund 500.000 Kubikmeter Holzfaserdämmplatten hat Gutex vergangenes Jahr produziert.174 Mitarbeiter sind heute bei Gutex beschäftigt, viele davon schon lange. Circa 100 von ihnen arbeiten verteilt auf vier Schichten in der Produktion. Zu den Beschäftigten zählen auch sechs Lehrlinge, die in drei Berufen ausgebildet werden. Das Unternehmen bewegt sich in einer Nische: Der Dämmstoffmarkt wird von Produkten aus Polystyrol (Styropor) und Mineralwolle dominiert, Dämmplatten aus Holz haben einen geschätzten Marktanteil von rund sieben Prozent, Tendenz steigend – „weil das Bewusstsein für nachhaltige Produkte am Wachsen ist“, so Claudio Thoma.
Auch die Branche der Holzfaserdämmstoffhersteller ist klein, etwa eine Handvoll Firmen gibt es in Europa. Gutex ist eine der beiden größten und produziert im Gegensatz zu seinen Wettbewerbern ausschließlich in Deutschland – am Firmensitz in Gutenburg. „Wir wollen gesunde Lebensräume schaffen“, so Claudio Thoma. Außerdem habe Holz weitere positive Eigenschaften: „Es schützt im Sommer vor Hitze und im Winter vor Kälte, bietet zusätzlich einen Schallschutz und ist diffusionsoffen, es besteht also keine Schimmelgefahr.“ Überall dort, wo traditionell viel Holz verbaut wird, macht Gutex gute Geschäfte. Das ist vor allem die Alpenregion. 70 Prozent des Umsatzes entfallen auf Deutschland, gefolgt von der Schweiz, Österreich, Südtirol, Frankreich sowie den Beneluxländern. Vertrieben werden die Produkte vor allem über circa 350 qualifizierte austoffhändler in diesen Ländern, rund 15 Prozent der Dämmstoffe liefert Gutex direkt an seine Industriekunden aus der Fertighausbranche. Nicht nur in Holz-, auch in Massivhäusern aus Stein werden Gutex-Produkte verbaut. „Wir sind in der Dachsanierung sehr stark“, sagt Claudio Thoma. Das Hauptgeschäft entfällt auf Wohnhäuser. Ein besonderes Beispiel ist das Freiburger Eugen-Keidel-Thermalbad, dessen rund 3.000 Quadratmeter großes Dach bei der Sanierung mit Gutex-Produkten gedämmt wurde. Der zweite große Geschäftsbereich sind Wärmedämmverbundsysteme für Fassaden, bei denen Putze verschiedener Hersteller verwendet werden können. Hier macht Gutex das Hauptgeschäft im Holzbau. Zu den Vorzeigeprojekten in diesem Bereich gehören das Forsthaus in St. Peter sowie das Mehrgenerationen-Wohnbauprojekt Rundacker in Staufen, bei dem mehrere viergeschössige Wohnhäuser in Massivbauholzweise erstellt wurden. Insgesamt bietet Gutex 14 verschiedene Produktfamilien von der Aufdach- bis zur Bodendämmplatte an. Das Holz kommt vor allem von Tannen und Fichten aus dem Schwarzwald. Etwa drei Viertel liefern regionale Sägewerke in Form von Hackschnitzeln; das restliche Viertel kommt als Rundholz von regionalen Forstbetrieben und wird auf dem Betriebsgelände entrindet und gehackt.
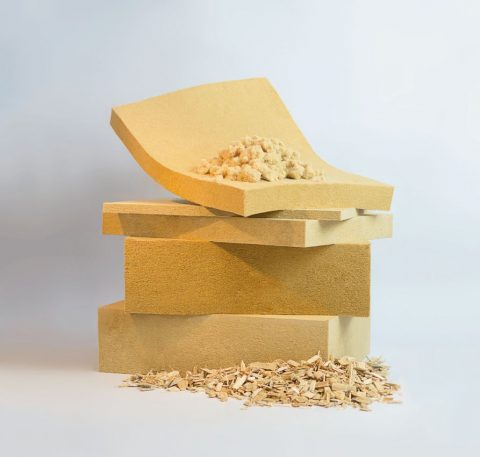
Die Ursprünge des Unternehmens: Um 1900 wurde auf dem heutigen Betriebsgelände ein E-Werk errichtet, das Strom für die umliegenden Gemeinden produzierte. Die mechanische Energie, die dabei freigesetzt wurde, nutzten die Eigentümer, um Holzschliff für die inzwischen stillgelegte Papierfabrik in Albbruck herzustellen. Claudio Thomas Urgroßvater Hugo Henselmann stieg in das Gutenburger Unternehmen ein und übernahm es um 1920. Sein Sohn Heinrich Henselmann experimentierte mit dem Holzschliff und produzierte 1932 als erstes mitteleuropäisches Unternehmen Holzfaserdämmplatten. Das war die Geburtsstunde von Gutex. „Er war ein Tüftler und Pionier“, sagt Claudio Thoma über seinen Großvater. Er selbst, ein Diplom-Ingenieur, hat die Geschäftsführung 2005 von seiner Mutter Karin Thoma-Komm übernommen. Ins Jahr 2005 fällt auch eine der größten Investitionen in der Unternehmensgeschichte, die der Grund dafür ist, dass sich der Umsatz seitdem etwa verdreifacht und die Mitarbeiterzahl etwas mehr als verdoppelt hat: Für circa 15 Millionen Euro wurde eine Anlage angeschafft, die Holzfaserdämmplatten mit einem homogenen Rohdichteprofil im Trockenverfahren herstellt. „Wir waren das erste Unternehmen weltweit, das das gemacht hat“, sagt Claudio Thoma. Inzwischen ist dieses Verfahren in der Branche etabliert. Damit können dickere, das heißt bis zu 30 Zentimeter starke, Dämmplatten hergestellt werden. Gleichzeitig verbraucht die moderne Anlage weniger Energie und arbeitet wirtschaftlicher als die herkömmliche, auf der im Nassverfahren maximal 2,5 Zentimeter starke Dämmplatten produziert werden können.
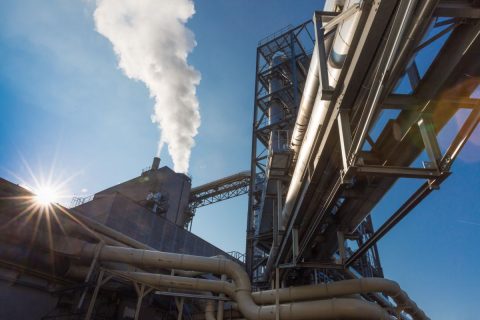
Inzwischen betreibt das Gutex Holzfaserplattenwerk vier verschiedene Produktionsanlagen. Die jüngste, ebenfalls rund 15 Millionen Euro teure Anlage für flexible Dämmstoffe wurde 2016 installiert. Die dort hergestellten flexiblen Dämmmatten wurden vergangenes Jahr von der Zeitschrift Öko-Test mit „sehr gut“ ausgezeichnet. Das Unternehmen selbst hat bereits 1994 ein Qualitäts- und ein Umweltmanagementsystem eingeführt. Heute ist Gutex nach den Normen DIN EN ISO 9001 und 14001 sowie EM AS II zertifiziert. Rund 50 Prozent des benötigten Stroms produziert das Unternehmen selbst – unter anderem mithilfe von Photovoltaikanlagen auf den Hallen des rund vier Kilometer entfernten Außenlagers im Kaitle sowie mit einem Gasblockheizkraftwerk auf dem Firmengelände in Gutenburg. Die dort entstehende Abwärme wird für das Trocknen der Hackschnitzel verwendet. Das Wasser, das ihnen entzogen wird, formt die von weitem sichtbaren Dampfwolken, die aus dem Fasertrockner entweichen.
Mae