Vom Kirchenfenster über die Leuchtwerbung zum Autoschiebedach – die Firma Borsi hat in ihrer Geschichte schon einige Richtungswechsel hingelegt. Der Trick: altes Knowhow laufend in neue Anwendungen einbringen.
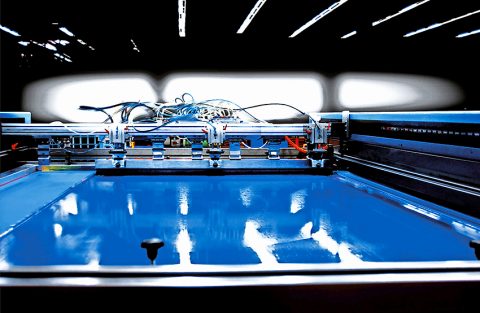
Schutterwald. Noch lässt sich nur erahnen, dass die krakeligen Linien auf der weißen Kunststoffplatte am Ende mal eine präzise Geometrie ergeben. Bislang erinnern sie eher an das verzerrte Bild auf einem Motiv-Luftballon, das sich erst „geraderückt“, wenn ausreichend Luft drin ist. Am Ende des sogenannten Tiefziehprozesses wird sich aus der Platte ein gewölbtes Lichtelement geformt haben, und entlang der Linien wird sich genau an den vorausberechneten Kanten ein durchscheinendes Muster bilden.
Um dieses Zusammenspiel der Materialien hinzubekommen – und jederzeit reproduzieren zu können, ohne Dutzende von neuen Anläufen zu benötigen – braucht es Erfahrung. Selbst heute lässt sich nicht alles am Computer vorausberechnen. Und Erfahrung hat die Borsi GmbH & Co KG in Schutterwald eine ganze Menge: Seit 1821 ist der heutige Kunststoffverarbeiter in Sachen Farben und Oberflächenbearbeitung unterwegs.
Farbe und Oberfläche sind denn auch die Konstanten in der 200-jährigen Firmengeschichte. Ansonsten war und ist Borsi ein Meister im Sich-neu-Erfinden. „Wir sind wohl das älteste Start-up Deutschlands“, umschreibt Peter Breer als geschäftsführender Gesellschafter diesen Umstand augenzwinkernd. Seit 2006 leitet der 54-Jährige das Unternehmen, zu dem er erstmals 1993 nach dem Studium stieß und zu dem der Kontakt nie abriss, auch wenn Breer zwischenzeitlich mal für andere Unternehmen tätig war: „Ich habe auch in dieser Zeit immer mit und für Borsi gearbeitet“, erklärt er seine lange Verbundenheit zum Traditionsunternehmen, das vor 200 Jahren unter seinem Gründer Jakob Anton Derndinger mit der Herstellung und Kolorierung von bleigefassten Kirchenfenstern begann.
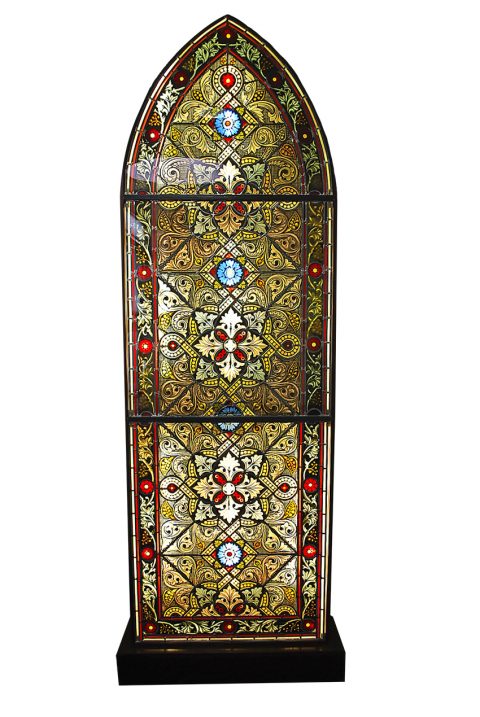
Als im beginnenden 20. Jahrhundert Marken immer mehr die Welt eroberten, brachte das Unternehmen seine Farben fortan auch auf Werbespiegeln etwa für Getränke- oder Seifenhersteller auf. Rund um den Ersten Weltkrieg wuchs das Portfolio um Skalen für Radios. Etliche Jahre später kamen dekorative Frontscheiben für Spielautomaten hinzu – bevor sie im Monitorzeitalter obsolet wurden.
Ende der 1960er-, Anfang der 1970er-Jahre ging Borsi mit der aufkommenden Kunststoffverarbeitung in die dritte Dimension und fertigte über fast zwei Jahrzehnte Displays und Produktständer für den Einzelhandel, bis immer mehr asiatische und osteuropäische Konkurrenz auf den Plan trat. Das Unternehmen suchte wieder nach neuen Einsatzfeldern für seine Technik und etablierte Ende der 1980er ein Verfahren, bei dem nun auch metallisch beschichtete Kunststoffe und Folien im bereits etablierten Tiefziehverfahren so erwärmt und umgeformt wurden, dass sie dabei lichtdurchlässig wurden. Bei Borsi die Geburtsstunde der gewölbten Leuchtwerbeschilder, die das Unternehmen nun schon seit Jahrzehnten für die Außenwerbung für Brauereien, Handelsunternehmen, Autohäuser und -hersteller fertigt. Im Treppenhaus des Firmensitzes in Schutterwald, in dem die Verwaltung wie auch die gesamte Fertigung sitzt, reiht sich eine renommierte Marke an die andere, von Warsteiner und Krombacher über VW bis Fiat und Lamborghini.
„Die Produktionstechniken an sich sind schon alt. Das Siebdruckverfahren zum Beispiel, mit denen wir die Farben auf die Fläche bringen, gibt es seit gut hundert Jahren“, erklärt Firmenchef Peter Breer. „Aber die Anwendungsmöglichkeiten kommen und gehen. Und unsere Aufgabe ist, immer dranzubleiben und mit etwas Fantasie neue Einsatzzwecke zu antizipieren.“
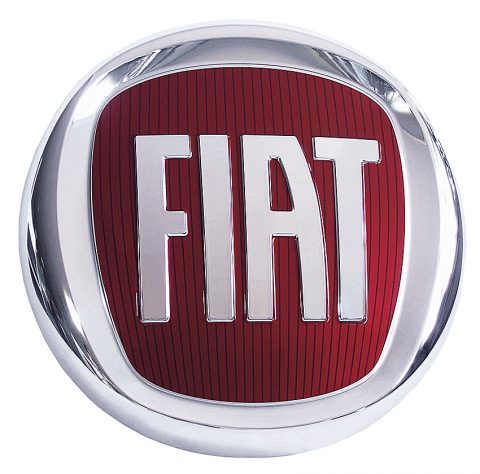
Unter dieser Maßgabe entwickelte sich seit den 2000ern die technische Produktschiene rasant weiter. Machte sie damals nur 15 bis 20 Prozent des Umsatzes aus im Vergleich zur dekorativen Schiene, hat sich das Verhältnis mittlerweile umgedreht. Borsi bedruckt und formt inzwischen auch in großen Stückzahlen Innenverkleidungen für Autos, Lkw und Industriespülmaschinen, macht Sitzschalen für Busse und Bahnen, stattet ganze Gebäude mit beleuchteten Fassadenelementen aus. Der Vorteil des Tiefziehverfahrens: „Wir können die Teile, im Unterschied zu spritzgussgefertigten, auch fräsen. Deshalb wird nicht für jede Produktvariante eine neue Form benötigt“, erklärt Breer. In einer Zeit des zunehmenden Variantenreichtums ist das ein Vorteil. Die Entwicklung zu mehr E-Mobilität spielt Borsi in die Karten. Um Gewicht zu sparen, setzen Autobauer verstärkt auch für außen auf Kunststoffteile. Für den gelben E-Scooter der Deutschen Post fertigt Borsi etwa Dach, Motorhaube und diverse andere Teile.
Sich ständig neu zu erfinden, ist eine echte unternehmerische Herausforderung, der man sich immer wieder stellen muss, erklärt Peter Breer. „Wir waren zum Beispiel lange eher handwerklich geprägt und mussten uns das industrielle Verständnis und die Prozesse für einen höheren Durchsatz erst erarbeiten.“ Wie ein Konditor, der statt 100 Torten plötzlich zehntausend genormte Brezeln backen muss, vergleicht es Breer.
Wie dem Rest der Wirtschaft kam auch Borsi die Coronapandemie ungelegen, man berappelte sich aber schnell. Mit seinen 130 Festangestellten und 15 Leiharbeitern peilt Peter Breer für 2021 einen Umsatz von 17 Millionen Euro an, um in den nächsten zwei, drei Jahren die 20-Millionen-Marke zu knacken. Als Familienunternehmen vor 200 Jahren gestartet, ist Borsi weiterhin ein inhabergeführtes Unternehmen – auch wenn der letzte Anteilseigner aus der ursprünglichen Gründerfamilie 2015 ausgeschieden ist.
uh
Bilder:
Maschine für Siebdrucke von rund drei auf vier Metern (oben). Kirchenfenster sind der Ursprung Borsis (Mitte). Leuchtwerbung für Fiat-Autohäuser (unten).