Seit Mitte 2018 fertigt die Sick AG in einer vernetzten Fabrik mit autonomen digitalen Produktions- und Steuerungsprozessen Sensoren. Sick ist damit ein Pionier in Deutschland. Die Presse hatte kürzlich Gelegenheit, die Fabrik in Freiburg-Hochdorf zu besichtigen.
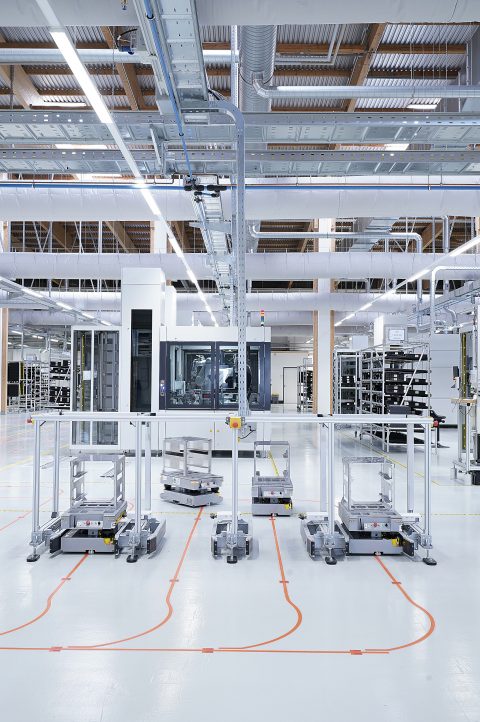
Der Begriff Industrie 4.0 ist in aller Munde, und Definitionen gibt es viele. Zum Beispiel: „Industrie 4.0 bedeutet dynamische, echtzeitoptimierte, sich selbst organisierende und unternehmensübergreifende Wertschöpfungsnetzwerke“, oder „Industrie 4.0 bezeichnet die intelligente Vernetzung von Maschinen und Abläufen in der Industrie mit Hilfe von Informations- und Kommunikationstechnologie“. Die Sick AG ist da konkreter. In der Beschreibung seiner neuen Fabrik führt das Unternehmen aus: „Industrie 4.0 steht für die intelligente Vernetzung von Entwicklung, Produktion, Logistik, Kunden und Partnern. Die dabei gewonnenen Daten sorgen für Transparenz im Prozess. Sie sind die Basis für weiterführende automatisierte Aktionen und ermöglichen eine optimierbare anpassungsfähige Wertschöpfung. Und das in Echtzeit. Dabei werden Anlagen autark und sind durch intelligente Vernetzung in der Lage, eigenständig auf ungeplante Situationen zu reagieren, also die Produktion an eine veränderte Auftragslage anzupassen.“
Wie das bei Sick funktioniert, hat das Unternehmen im April auf der Hannover Messe anhand eines dort aufgebauten Produktionsmoduls, eines Films und mit Videoübertragungen ins Werk vorgeführt. Das Interesse des Publikums war groß, die Reaktionen reichten von Begeisterung bis zu kompletter Irritation, berichtet Bernhard Müller, in der Geschäftsführung von Sick für Industrie 4.0 zuständig.
Das Unternehmen
Sick ist einer der weltweit führenden Hersteller von Sensoren und Sensorlösungen für industrielle Anwendungen. Das 1946 von Erwin Sick gegründete Unternehmen mit Stammsitz in Waldkirch zählt zu den Technologie- und Marktführern und ist mit mehr als 50 Tochtergesellschaften und Beteiligungen sowie zahlreichen Vertretungen rund um den Globus präsent. Im vergangenen Jahr beschäftigte das Unternehmen knapp 10.000 Mitarbeiter weltweit und erzielte 1,6 Milliarden Euro Konzernumsatz.
Doch was wird in der Fabrik wie gefertigt? Produziert werden Lichtschranken, Lichttaster und Kontrastsensoren der neuesten Generation. Sie bestehen aus bis zu 250 Teilen, ihre Dimensionen bewegen sich, bildhaft ausgedrückt, zwischen Streichholz- und Zigarettenschachtelgröße. Derzeit kommen fünf Produktfamilien aus der Fabrik, künftig sollen es zwölf sein, die über die nächsten Jahre entwickelt werden. Über 500.000 Produktvarianten in Losgrößen von eins bis zu maximal 30 je nach Variante werden hergestellt. Dafür stehen zwölf vollautomatisierte Produktionstechnologiemodule, vier manuelle Arbeitsplätze und ein hybrider Arbeitsplatz zur Verfügung. Prozesse können also vollautomatisch, manuell oder hybrid ausgeführt werden. In dem zellulär angeordneten Produktionsprozess kann die Reihenfolge der Modulnutzung je nach Anforderung variieren. Die Produkte beziehungsweise Produktfamilien müssen nicht alle, sondern nur die für ihre Herstellung notwendigen Module durchlaufen, dies aber in der richtigen Reihenfolge. Die Materialzufuhr erledigen „automatic guided carts“ (AGCs). Wie von Geisterhand bewegt, so scheint es dem laienhaften Betrachter, fahren sie die Module mithilfe von Sensoren an, die sich an auf dem Boden angebrachten Streifen orientieren. Alle Abläufe, so demonstrieren die für die Produktion verantwortlichen Ingenieure Volker Zaeh und Joachim Schultis, werden von einer hochleistungsfähigen Software gesteuert, die bei Sick entwickelt wurde. Als Basis diente das Wissen, das Sick über Jahre im Produktionsmittelbau gewonnen hatte. In der Software sind alle Informationen zum jeweiligen Auftrag hinterlegt, beispielsweise Produkteigenschaften, Stückzahl und Angaben dazu, welche Fertigungsschritte an welchem Modul notwendig sind. Das System sendet die Informationen an die Maschinen und erhält umgekehrt ständig Rückmeldungen. Alle Akteure – Sensoren, Maschinen und Menschen – sind dezentral organisiert, vernetzt und tauschen sich kontinuierlich aus. Alle Daten der 4.0 Factory werden in Echtzeit in der Cloud gesammelt. So entsteht ein virtuelles Abbild der Produktion. Die wichtigsten Leistungskennzahlen daraus werden in Form eines cloudbasierten Dashboards für die Anlagenmanager visualisiert. Diese können so maximale Transparenz über die aktuelle Leistungsfähigkeit der Produktion und alle Logistikprozesse gewinnen. Jedes Modul hat dabei einen sogenannten digitalen Zwilling, der mit den anderen Zwillingen interagiert. In den gesamten Prozess sind auch Kunden und Lieferanten einbindbar.
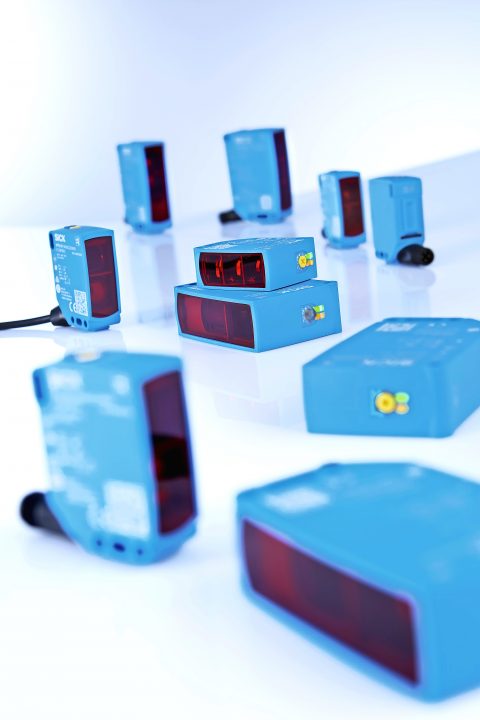
Zwei Jahre Vorbereitungs- und Aufbauzeit (die Maschinen stammen vom bayerischen Hersteller Baumann) waren nötig, bis die Produktion beginnen konnte. Und „es funktioniert“, sagt Bernhard Müller. Besonders beeindruckend ist, dass sehr schnell vielfältige und individuelle Kundenwünsche berücksichtigt und selbst kleine Stückzahlen „on demand“ produziert werden können. Und dies, so die Sick-Mitarbeiter, bei Kosten, die denen einer Massenproduktion gleichen. Die ganze Fertigung beschäftigt derzeit 13 Mitarbeiter (neun Werker und vier Techniker) im Einschichtbetrieb. Mittelfristig will man im Dreischichtbetrieb arbeiten. Die maximale jährliche Ausbringungsmenge wird dann bei 1,2 Millionen Stück liegen. Die Durchlaufzeit für eine Bestellung liegt momentan bei durchschnittlich fünf bis sechs Tagen. Auch vier Stunden als schnellstes Resultat sind schon möglich.
Das ganze Modell ist Sick-spezifisch. Bernhard Müller betont ausdrücklich, dass es keine allgemeingültige Industrie 4.0-Lösung gibt. Die Sick-Lösung ist kaum auf andere Produkte wie zum Beispiel Autos oder Kühlschränke übertragbar. Die Fabrik arbeitet natürlich mit einer Unzahl von Sick-Sensoren, die in die Module eingebaut sind. Und sie wäre auch ohne die neuen Produktlinien, die hier hergestellt werden, nicht denkbar. Deren Konstruktion ist ebenfalls auf die neue Fertigungsweise angepasst. Seinen Kunden und anderen Interessenten hat Sick auf der Hannover Messe vor allem den Mehrwert demonstrieren wollen, den man über eine 4.0 ausgerichtete Fertigung erzielen kann. Zu den Mehrwerten gehört auch die Intelligenz der Sensorik, beispielsweise in Visionsystemen oder Barcodelesern. Die ganze Anlage ist also auch eine Art Werbung für die technologische Führungsrolle von Sick. Nach den Investitionen für die Fabrik gefragt, antwortet Müller: „Das sagen wir nicht.“ Aber – so viel will er doch preisgeben – dass fünf neue (zukünftig zwölf) Linien traditioneller Fertigungstechnologie teurer gewesen wären, als die 4.0 Fabrik. Sie wird sich sehr viel schneller amortisieren, als der üblicherweise zehn Jahre dauernde Fertigungszyklus eines Produktes.
Die Anlage kann laut Müller als die erste 4.0-fähige Produktion in Deutschland gelten, zumindest kennt er kein anderes Beispiel. Sie repräsentiert den Beginn einer neuen Ära. Müller und sein Team stellen dazu gerne einen Vergleich an: „Die Industrie ist derzeit noch in der ersten Grundschulklasse in der 4.0 Entwicklung. Täglich lernen wir dazu. Bis zum Gymnasium oder gar bis zum Abitur ist es noch weit.“
Text: Ulrich Plankenhorn