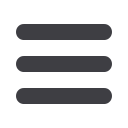
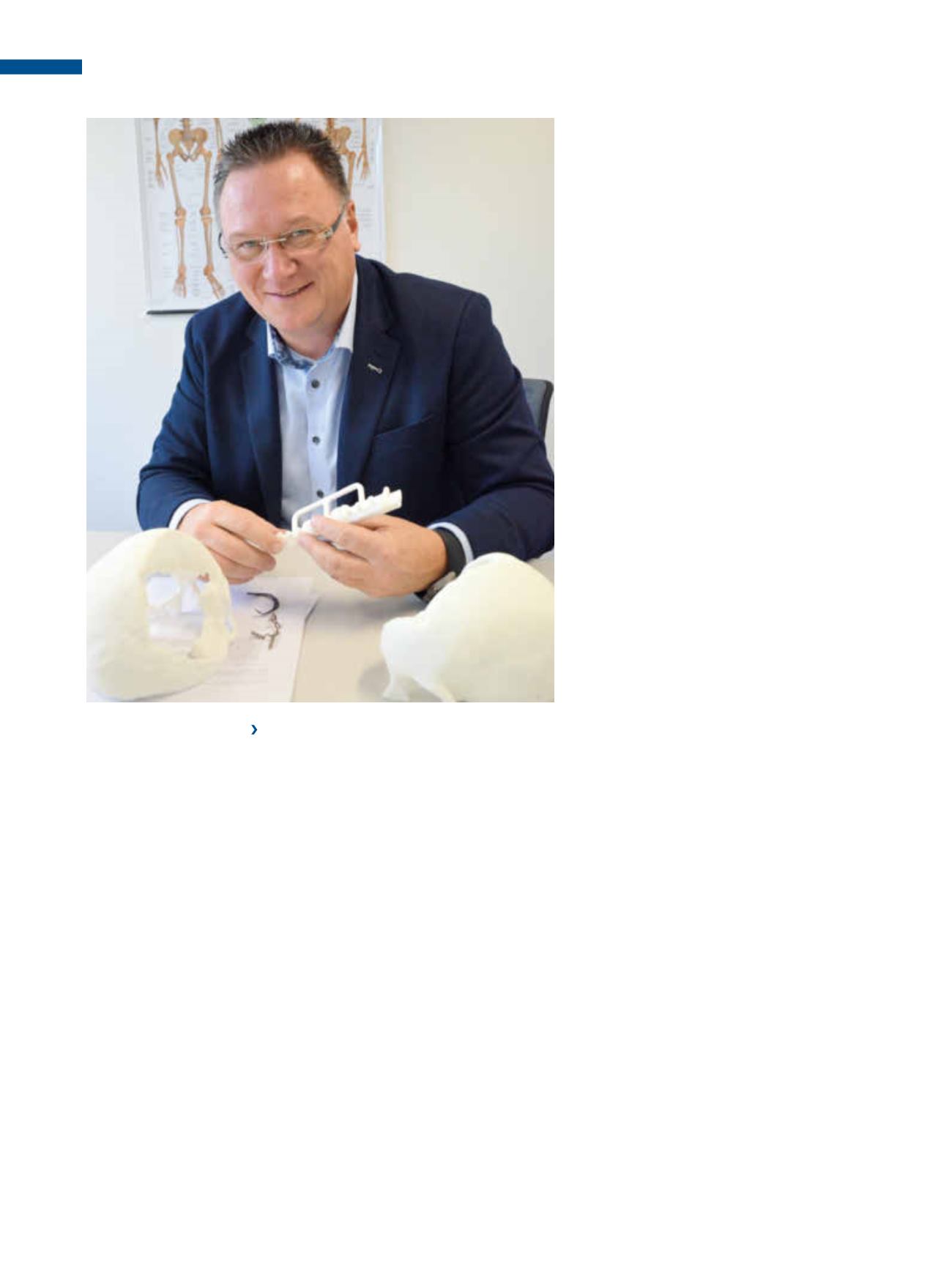
Wirtschaft im Südwesten
1 | 2018
8
titel
nehmen mit der neuen Technologie auch individu-
alisierte Implantate her, die neben den technischen
Herausforderungen die strengen Auflagen für Medi-
zinprodukte bewältigen müssen. Die heute mehr als 20
Drucker stehen in den Produktionshallen in Mühlheim
an der Donau, Tuttlingen und Freiburg – grau-weiße
Kästen mit Steuerungsbildschirmen, manche erinnern
an Kaffee- oder Getränkeautomaten. Hinter grün ge-
tönten Schutzscheiben kann man erkennen, wie Laser
blitzend über dünne Schichten aus Titanpulver jagen.
„Wir haben Kooperationen mit praktisch allen großen
Herstellern“, sagt Reinauer. Das Unternehmen ist an
Forschungsprojekten beteiligt, die das Bundesfor-
schungsministerium (BMBF) finanziert; die Techniker
experimentieren mit druckfähigen Materialien wie etwa
Polymeren, die sich im Körper nach und nach auflö-
sen, oder Keramik. Sie entwickeln Software weiter und
verkleinern in den Druckern die Bauräume, um teures
Pulver zu sparen. „Wir haben Millionen investiert“, sagt
der geschäftsführende Gesellschafter Christian Leibin-
ger. „Am Anfang war es mehr ein Forschen, da waren
wir schon etwas ungeduldig – aber dann ging es ganz
schnell.“ Heute mache das Familienunternehmen mit
1.200 Mitarbeitern bereits knapp zehn Prozent seines
Umsatzes mit 3D-Druck, Tendenz steigend: „Das ist die
absolute Zukunft im Implantatbereich“, sagt Leibinger.
S
eit Januar 2017 fördert das BMBF auch das Pro-
jekt „Medizintechnik International und Digital
(MinD)“ der Tuttlinger Clusterinitiative Medical
Mountains. Ziel sind internationale Kooperationen von
kleinen und mittleren Unternehmen aus der Region zum
Thema 3D-Druck. Jenseits der Medizintechnik werde
3D-Druck von den Unternehmen in der Region insge-
samt „noch verhalten genutzt“, sagt Sebastian Wieken-
berg, Referent Innovation und Technologie bei der IHK
Südlicher Oberrhein – aber das Interesse wachse. Der
erste 3D-Drucker sei schon 1984 entstanden, doch
gerade jetzt bekomme das Thema viel Aufmerksam-
keit. Dafür sorgten sowohl die inzwischen nur noch
wenige hundert Euro teuren Geräte für zuhause, als
auch die industriellen Neuerungen. „Die Technolo-
gie ist noch nicht am Ende der Entwicklung und wird
immer interessanter – auch für kleinere und mittlere
Unternehmen“, sagt Wiekenberg. Diese sollten vor
einer Anschaffung aber genau überlegen, wofür und
wie oft sie einen 3D-Drucker einsetzen wollen, wel-
ches technische Verfahren dafür sinnvoll ist und wie
viel Arbeit in Einrichtung und Nachbearbeitung steckt
– zumal industrielle Systeme deutlich fünfstellige Be-
träge kosten, so Wiekenberg. Auch die entsprechende
CAD-Software sei wichtig, ergänzt sein Kollege Philipp
Klemenz, schließlich brauche der Drucker eine digi-
tale 3D-Vorlage. Für Prototypen und Kleinstserien,
da sind sich die beiden IHK-Berater einig, könne ein
3D-Drucker in vielen Unternehmen Sinn ergeben.
Auch Sunita Patel, Geschäftsführerin des Bereichs
Innovation bei der IHK Hochrhein-Bodensee, sieht
viel Potenzial. Die IHK wolle 2018 einen Schwerpunkt
auf Digitalisierung legen und über Chancen der 3D-
Technologie informieren.
W
ir drucken Prototypen aus dem wertvollen
Kunststoff ABS“, sagt Klaus-Peter Grasse,
„die funktionieren wirklich und fallen nicht
gleich auseinander, wenn man sich mal draufsetzt.“ Das
ist wichtig – der Ingenieur ist Leiter der Produktent-
wicklung beim Büromöbelhersteller Sedus Stoll (siehe
auch Seite 40). Das Unternehmen mit Sitz in Waldshut
machte 2016 einen Umsatz von 188 Millionen Euro und
beschäftigt rund 900 Mitarbeiter. Die Entwicklungsab-
teilung arbeitet im benachbarten Dogern. Im Unter-
geschoss liegen die Werkstätten, im Stock darüber
sitzen Designer an Computern, auf ihren Bildschir-
men drehen sie 3D-Modelle eines neuen Bürostuhls.
In einer kleinen Kammer neben ihrer Teeküche steht
der hauseigene 3D-Drucker, er arbeitet mit „Fused
Deposition Modeling“, einem Verfahren, bei dem ein
drahtförmiger Kunststoff verflüssigt und Schicht für
Schicht aufgetragen wird. Alle Konstrukteure können
ihre Daten direkt auf den Drucker schicken.
„Wenn ein Entwurf fertig ist, drucken wir ein Modell im
Maßstab eins zu fünf“, erklärt Grasse und hält einen
kleinen Stuhl komplett aus Kunststoff in der Hand.
„Das schauen wir uns dann an – so bekommen wir
einfach ein besseres Gefühl für die Proportionen als am
flachen Bildschirm.“ Für spätere Eins-zu-eins-Design-
Frank Reinauer von KLS
Martin erklärt anhand von
gedruckten 3D-Modellen,
wie sein Unternehmen die
neue Technologie nutzt.
»So bekommen
wir ein besseres
Gefühl für die
Proportionen
als am flachen
Bildschirm«
Bild: Goebel