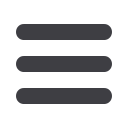
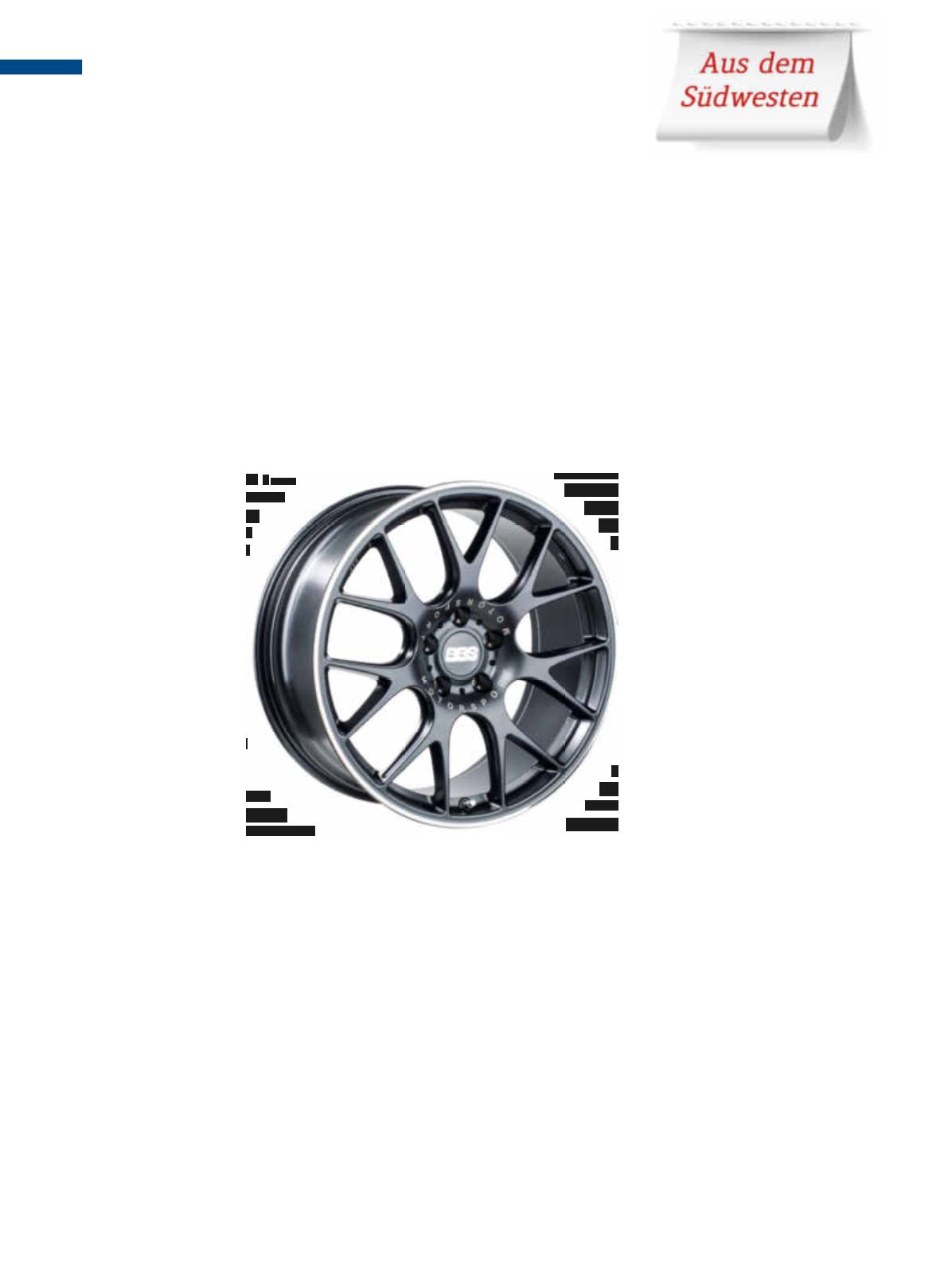
Wirtschaft im Südwesten
11 | 2017
72
DIE LETZTE SEITE
BBS GmbH
Räder aus Schiltach
In unserer Rubrik „Aus dem Südwesten“ stellen wir
Produkte vor, die viele kennen, von denen aber wenige
wissen, dass sie in der Region hergestellt werden.
Diesmal: Leichtmetallräder für Pkw der BBS GmbH
in Schiltach.
Mit Weltmeistertitel
Der Name BBS steht für Heinrich
B
aum-
gartner, Klaus
B
rand und
S
chiltach im
Schwarzwald. Hier gründeten die
beiden im Jahr 1970 das Unter-
nehmen und starteten mit dem
Fertigen von Karosserieteilen
aus Kunststoff. Drei Jahre
später konstruierten sie
ein neuartiges, dreiteili-
ges Motorsportrad, das
„RSI“-Rad, die erste und
inzwischen eine von vielen
technologischen Neuerun-
gen aus Schiltach. Es sollte
den Durchbruch für die Firma
bedeuten und sie international
bekannt machen. Als Michael
Schumacher 1994 und 1995
Formel-1-Weltmeister mit Benetton
Renault und später fünfmal mit Ferrari
wurde, fuhr er auf Rädern von BBS. „Davon
profitieren wir heute noch“, sagt Erwin Eigel,
Bereichsleiter Aftermarket bei der BBS GmbH.
Die Motorsportsparte firmiert allerdings seit
der Umstrukturierung im Zuge der Insolvenz im
Jahr 2012 als BBS Motorsport GmbH mit Sitz
in Haslach im Kinzigtal und gehört zu einem
japanischen Konzern. Die BBS GmbH selbst,
die nach wie vor Leichtmetallräder für Pkw
fertigt, ist Teil einer südkoreanischen Industrie-
gruppe. Am Hauptsitz von BBS in Schiltach so-
wie am Standort in Herbolzheim sind rund 730
Mitarbeiter und 23 Auszubildende beschäftigt.
Neun weitere arbeiten bei BBS of America in
Georgia.
Text: mae, Bild: BBS GmbH
Für Porsche, Audi und Bentley
Die BBS GmbH produziert etwa eine Million Räder pro Jahr und setzte 2016
knapp 90 Millionen Euro um. Damit gehört sie im internationalen Vergleich zu
den kleinen Räderherstellern. „Wir zählen aber zu den bekanntesten Rädermar-
ken im Premiumsegment weltweit“, sagt Erwin Eigel. Er verweist auf die zahlrei-
chen Preise, mit denen BBS seit 1995 regelmäßig ausgezeichnet wird – darunter
sind der „Best Brand“ der Zeitschriften Auto Motor Sport und Sport Auto sowie
der „Theo award“ der Automagazine Tuning und VW Speed. Und die BBS GmbH
wächst: Seit der Insolvenz vor fünf Jahren hat sie Umsatz und Mitarbeiterzahl in
etwa verdoppelt. 85 Prozent der Fertigungskapazität wird zurzeit für sogenannte
Erstausrüster, also Automobilhersteller, verwendet. Größter Kunde ist Porsche,
dicht gefolgt von Audi. Dazu kommen Mercedes-AMG, Bentley, BMW Alpina und
seit Kurzem Lamborghini. 15 Prozent der Kapazitäten entfallen auf den Bereich
Aftermarket, das sind Reifen- und Autohändler sowie Kfz-Werkstätten, die die
Räder unter der Marke BBS vertreiben. Im Zuge der geplanten Kapazitätserwei-
terung soll dieser Bereich auf 20 Prozent wachsen.
In die Breite gezogen
BBS stellt Räder in insgesamt 555 verschiedenen Ausfüh-
rungen her. Sie teilen sich in die Produktsegmente Schmie-
deräder (Forged Line), Flow-Forming-Räder (Performance
Line) und Gussräder (Design Line) auf. Das bekannteste ist
das „CH-R“-Rad (siehe Bild) aus der Performance Line. Es
verfügt zudem über die meisten Ausführungen, nämlich
über 41. Zwischen 20.000 und 25.000 Stück werden pro
Jahr produziert. Im Werk in Schiltach wird das Rad erst im
Niedriggussverfahren aus einer Alulegierung gegossen
und dann mit Röntgenstrahlen durchleuchtet und
so auf Fehler geprüft. In der Wärmebehand-
lung wird es mehrere Stunden lang erhitzt.
So wird es fester und damit länger haltbar.
Nach dem Abschrecken im Wasserbad wird
das „CH-R“-Rad – so wie alle Typen der
Performance Line – im sogenannten Flow
Forming abgestreckt, das heißt in die Breite
gezogen. In der mechanischen Fertigung
werden anschließend unter anderem die
Lochkreise zum Montieren am Pkw in die
Räder gebohrt. Hinterfräsungen, also Aus-
höhlungen, an den Speichen reduzieren zu-
dem das Gewicht. Die geprüften Räder bringen
Lkw nach Herbolzheim. Dort werden sie lackiert,
der Schriftzug wird hinein gelasert und der Anfahr-
schutz aus Edelstahl montiert. Dann werden die Räder
verpackt, gelagert und an die Kunden versendet.